How Plastic Nameplates Enhance Customer Experience in Service Roles
Exactly How Plastic Nameplates Are Made: A Comprehensive Overview to Their Manufacturing Refine
The production of plastic nameplates involves a number of specific actions, beginning with the option of ideal products to the final finishing touches. Each stage is essential, guaranteeing the item meets certain demands for longevity and aesthetics. Numerous production strategies play a considerable role in crafting these nameplates. Understanding these processes can clarify the complexities behind what might appear like an easy item. What elements add to the quality and personalization of these nameplates?
Recognizing Plastic Products Used for Nameplates

The Layout Refine: From Principle to Prototype
The design procedure for plastic nameplates starts with a clear concept that guides the general creation. Designers collaborate with clients to define the function, style, and details requirements of the nameplate. This preliminary stage consists of conceptualizing sessions, sketching ideas, and picking colors and fonts that align with branding goals.Once the principle is established, developers make use of computer-aided style (CAD) software program to develop thorough digital depictions. These prototypes enable for visualization and adjustments prior to moving on. Comments from stakeholders is integral during this phase, as it assists fine-tune the style to satisfy expectations.After settling the electronic prototype, a physical version may be generated, frequently via strategies like 3D printing. This tangible depiction enables more assessment of appearances and capability. On the whole, the layout procedure is an important action that lays the structure for the reliable production of high-grade plastic nameplates.
Cutting and Shaping the Plastic
In the cutting and shaping phase of plastic nameplate manufacturing, the choice of materials plays a vital duty in establishing the end product's top quality and resilience (Plastic Nameplates). Various accuracy reducing techniques, such as laser cutting and CNC machining, guarantee that the plastic is formed with precision and uniformity. This combination of careful material choice and advanced reducing approaches is crucial for producing premium nameplates
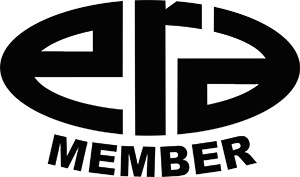
Material Option Process
Selecting the ideal product is vital for generating premium plastic nameplates. Various kinds of plastics are readily available, each offering unique benefits and characteristics. Typical selections include acrylic, polycarbonate, and PVC. Polymer is favored for its clearness and UV resistance, making it optimal for exterior applications. Polycarbonate, known for its longevity and effect resistance, is suitable for environments that require improved protection. PVC is usually chosen for its cost-effectiveness and versatility in layout. The option process also thinks about factors such as surface, thickness, and color coating, which can significantly influence the last look and performance of the nameplate. Eventually, the picked product needs to align with the intended use and aesthetic goals of the plastic nameplate.
Accuracy Cutting Methods
While picking the proper product prepares, accuracy cutting strategies play an essential duty fit the plastic nameplates into their last types. Numerous methods, including laser cutting, CNC milling, and die reducing, are utilized to achieve accuracy and consistency. Laser cutting makes use of focused light to generate tidy sides and complex layouts, suitable for complex patterns. CNC milling supplies flexibility by eliminating excess product with precision, suiting various densities and forms. Die cutting, on the other hand, enables automation of consistent items, boosting efficiency. Each technique is picked based upon the design specs and the desired finish, making certain that the final product satisfies quality standards and client expectations while maintaining longevity and visual charm.
Printing Techniques for Personalization
How can suppliers attain exact and dynamic styles on plastic nameplates? The solution exists in numerous printing techniques customized for customization. Digital printing has actually acquired appeal because of its capacity to create high-resolution photos and intricate designs directly onto plastic surface areas. This approach allows for quick turnaround times and very little arrangement costs, making it excellent for short runs and customized orders.Screen printing remains an additional commonly used strategy, specifically for bigger quantities. It entails developing a pattern and applying layers of ink, resulting in abundant colors and sturdiness. UV printing, which uses ultraviolet light to heal the ink, is likewise effective, providing exceptional adhesion and resistance to fading.Additionally, pad printing offers versatility for irregularly shaped nameplates, allowing for thorough styles on tough surfaces. These printing methods allow producers to meet diverse client needs while ensuring high quality and long life in their plastic nameplate products.
Surface Area Therapies and Finishing Options

Top Quality Control Measures in Production
Ensuring the highest criteria of quality assurance throughout the production of plastic nameplates is necessary for keeping product integrity and client complete satisfaction. Manufacturers apply extensive inspection protocols at numerous phases of the production process. Raw materials undergo thorough screening to validate they meet requirements for toughness and color consistency. i was reading this During the molding stage, automated systems monitor criteria such as temperature level and stress to avoid defects.In enhancement, aesthetic inspections are conducted to determine any surface flaws or imbalances. Once the nameplates are produced, they undergo functional tests, including adhesion tests for printed elements and tension examinations for toughness. Quality control groups often utilize analytical sampling techniques to assess batches, making certain that any kind of inconsistencies from criteria are immediately resolved. This detailed strategy not just improves product high quality yet additionally cultivates count on with customers, attesting the supplier's dedication to excellence in every nameplate produced.
Packaging and Distribution of Finished Nameplates
The product packaging and distribution of completed plastic nameplates are vital action in guaranteeing they reach consumers in excellent condition. Different packaging materials are selected to secure the nameplates throughout transit, while shipping techniques are thoroughly selected based on efficiency and cost-effectiveness. In addition, effective storage space remedies are applied to preserve quality till the nameplates are provided.
Packaging Products Used
When dispersing ended up plastic nameplates, picking proper packaging materials is vital to guarantee their defense during transportation. Generally utilized products consist of bubble wrap, foam padding, and cardboard boxes, all designed to cushion the nameplates against influences and shocks. Bubble cover supplies an adaptable barrier, while foam cushioning assurances that nameplates continue to be firmly in position, lessening the threat of scrapes or damage. In addition, strong cardboard boxes are used to have the nameplates, providing architectural support and defense from exterior aspects. Tags might be put on suggest taking care of instructions or breakable components, even more enhancing safety throughout transportation. Overall, using high-quality product packaging products substantially adds to the honesty and discussion of the ended up plastic nameplates upon arrival at their destination.
Delivering Techniques Used
Efficient distribution of ended up plastic nameplates counts on numerous delivery methods that ensure safe and prompt shipment. Business commonly use messenger services, freight delivery, and postal solutions, depending upon the dimension, weight, and location of the bundles. For neighborhood deliveries, messenger solutions offer quick transit, guaranteeing nameplates reach customers quickly. For bigger orders, products shipping is favored, using vehicles or shipping containers to transfer bulk amounts successfully. Post offices act as a cost-efficient option for smaller deliveries, specifically for residential distributions. All shipping methods focus on safety packaging to stop damages during transportation. Tracking systems are additionally made use of to check shipments, providing clients with real-time updates and reassurance regarding the status of their orders.
Storage Solutions Implemented

Frequently Asked Inquiries
What Kinds Of Businesses Frequently Use Plastic Nameplates?
Plastic nameplates are commonly made use of by different companies, including offices, hospitals, institutions, and factories. These nameplates offer crucial features such as recognition, info display screen, and branding, contributing to business effectiveness and expert look throughout varied atmospheres.
How much time Does the Entire Production Process Take?
The manufacturing process duration differs based on intricacy and quantity, typically varying from a couple of days to several weeks. Aspects affecting this timeline include style authorization, product schedule, and manufacturing techniques utilized by the business.
Can Plastic Nameplates Be Recycled After Usage?
Plastic nameplates can be reused, supplied they are made from recyclable materials. The availability of recycling programs and local guidelines might influence their recyclability. Appropriate disposal techniques are vital to assure effective recycling.
What Are the Environmental Influences of Plastic Nameplate Production?
The environmental effects of plastic nameplate production include carbon discharges, resource depletion, and pollution from manufacturing processes. Plastic Nameplates. Additionally, improper disposal adds to plastic waste, adversely affecting communities and wild animals, highlighting the requirement for lasting practices
Are There Any Safety Interest In Plastic Nameplates?
Safety and security concerns concerning plastic nameplates mainly involve possible chemical direct exposure during manufacturing and the threat of products deteriorating over time, which might cause dangerous substances being launched, impacting both human health and wellness and the environment. While numerous products can be used for nameplates, plastic remains go to these guys a preferred selection due to its adaptability and resilience. In the cutting and forming phase of plastic nameplate production, the choice of materials plays a crucial duty in figuring out the final item's top quality and toughness. Selecting the appropriate material is vital for producing premium plastic nameplates. While choosing the proper product lays the groundwork, precision cutting techniques play a necessary duty check my source in forming the plastic nameplates into their final forms. When dispersing finished plastic nameplates, selecting proper packaging materials is necessary to guarantee their protection during transit.